Modular homes have become an increasingly popular choice in the housing market, offering a streamlined construction process, cost efficiency, and high standards of quality. Unlike traditional homes built on-site, modular homes are manufactured in controlled factory environments, which minimizes weather delays, reduces waste, and maintains precision in construction. However, the total cost of a modular home is influenced by multiple complex factors. This article provides an in-depth look at the costs involved, from initial design to transportation and final assembly, giving potential buyers and investors a clear understanding of what to expect.
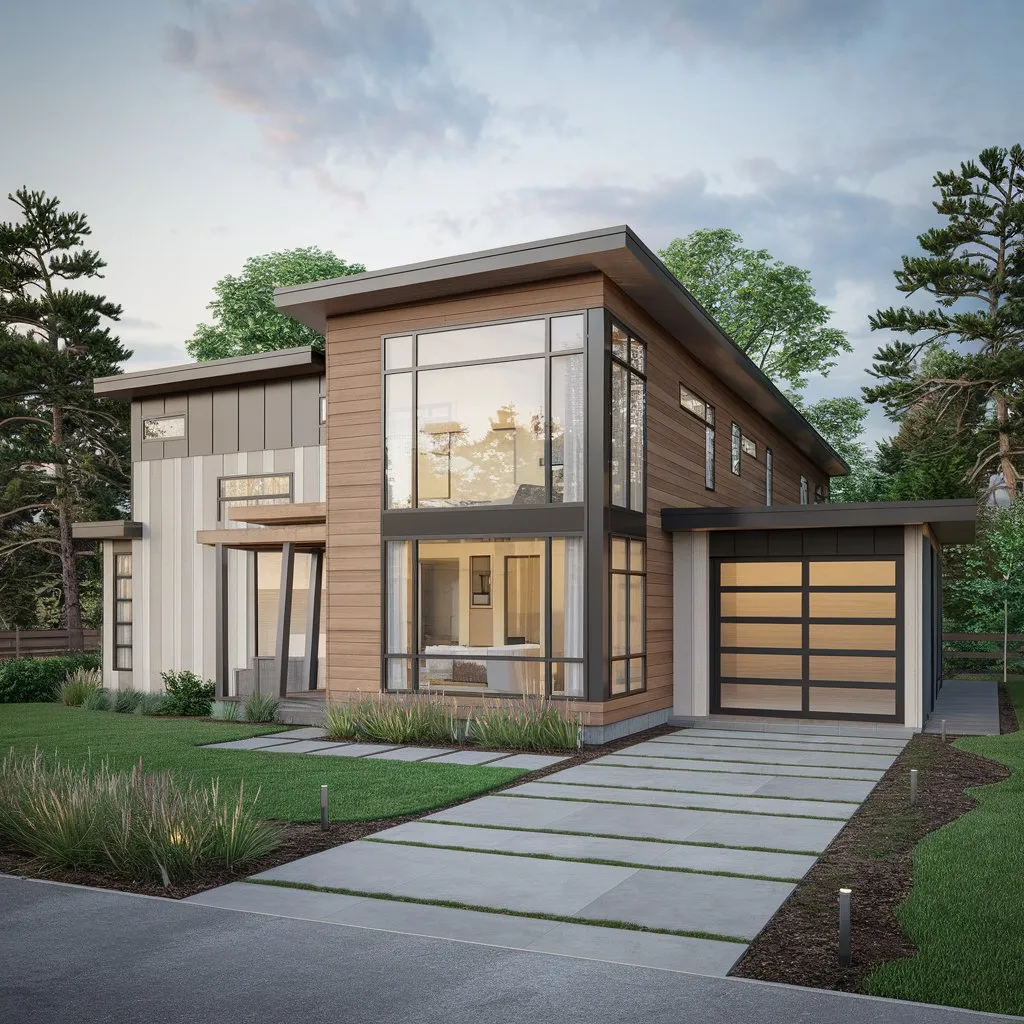
Key Components of Modular Home Costs
1. Material Costs
- Home Structure: The primary structure of a modular home typically includes wooden or steel framing and reinforced exterior panels. Steel framing, though more expensive, offers enhanced durability and resistance to pests and environmental damage, making it a preferred choice in regions prone to natural disasters.
- Walls and Roofing: The type of insulation used in walls and roofing significantly impacts energy efficiency. High-grade insulation materials like closed-cell spray foam and rigid foam panels, while costlier, can drastically reduce heating and cooling expenses, contributing to long-term savings.
- Windows and Doors: Double- or triple-glazed windows with Low-E (low-emissivity) coatings are preferred for their insulation properties and energy efficiency. Additionally, well-insulated doors with solid-core construction add to the home’s efficiency and security, although they come at a higher upfront cost.
- Flooring Options: Flooring selections can range from luxury vinyl tile, engineered hardwood, to ceramic and porcelain tiles, each with distinct price ranges and maintenance needs. Engineered wood and ceramic tiles offer durability and appeal, while being cost-effective compared to premium hardwood.
- Plumbing Fixtures: High-end plumbing fixtures from brands like Kohler or Grohe offer advanced water-saving technologies and durability, though they come at a premium. Choosing mid-range fixtures can help balance quality and cost.
2. Design and Engineering Costs
- Architectural Drawings: Precise architectural plans are essential to modular construction, ensuring that each module fits together seamlessly on-site. Costs vary based on the complexity of the design and any customization requests. For example, designs with complex rooflines or multi-level layouts require additional engineering input, adding to the cost.
- Interior Design: Modular homes offer customization, allowing homeowners to choose finishes, layouts, and decor details. Costs increase with custom cabinetry, built-in storage, and high-end fixtures, but opting for standardized or semi-custom interiors can help manage expenses.
3. Manufacturing Costs
- Manufacturing Processes: The factory setting allows for an efficient assembly line approach, but higher standards in precision and quality control add to manufacturing costs. Homes are generally built in climate-controlled factories, which allows for year-round construction but requires specialized equipment and skilled labor.
- Quality Control: Modular homes are rigorously tested to meet both factory standards and local building codes. Premium manufacturers often conduct additional inspections, which can ensure a long-lasting product but at a higher cost.
4. Transportation Costs
- Distance to Site: Transportation costs vary based on the site’s distance from the manufacturing facility. Moving oversized loads, such as large modules, across state lines may require special permits and escort vehicles, adding significant fees.
- Weight and Size of Modules: Heavier or more complex modules, such as those with additional structural reinforcements or high-end materials, will incur higher shipping costs. For larger modular homes, multiple shipments may be necessary.
5. Installation Costs
- Labor: On-site assembly requires skilled labor, often including electricians, plumbers, and carpenters to complete the final setup. Wages can vary based on local labor rates and the complexity of the home’s design.
- Equipment: Installation of modular homes requires specialized equipment like cranes to position and secure modules. Renting a crane and associated equipment can significantly increase costs, especially in hard-to-access locations.
- Utility Connections: Utility hookup fees vary depending on local regulations and infrastructure availability. Connections to utilities like water, electricity, and sewage may require additional fees, especially in remote areas lacking established infrastructure.
6. Additional Expenses
- Permits and Approvals: Obtaining permits and zoning approvals is a mandatory cost that varies by jurisdiction. For modular homes, it’s essential to meet local codes, which may require additional inspections and certifications, influencing the final cost.
- Site Preparation: Preparing the site can include grading, laying the foundation, and ensuring vehicle access for installation. Some sites may also require drainage solutions, retaining walls, or landscaping, which are additional expenses to consider.
Factors Influencing Modular Home Costs
- Home Size: Larger homes require more materials, more manufacturing time, and greater transportation logistics, all of which increase the overall cost.
- Design Complexity: Homes with custom layouts, multiple stories, or intricate architectural details require more precise engineering and manufacturing, which escalates costs.
- Material Quality: Premium materials not only enhance the aesthetic and longevity of the home but also contribute to energy efficiency, reducing utility bills over time. However, they come with a higher initial investment.
- Location of Build Site: Remote locations with difficult access can increase both transportation and installation expenses. Additionally, utility hookups and site preparation tend to be costlier in rural areas without established infrastructure.
- Manufacturer Choice: The reputation, expertise, and location of the manufacturer influence costs. High-end manufacturers typically offer advanced customization and quality assurance but at a higher price.
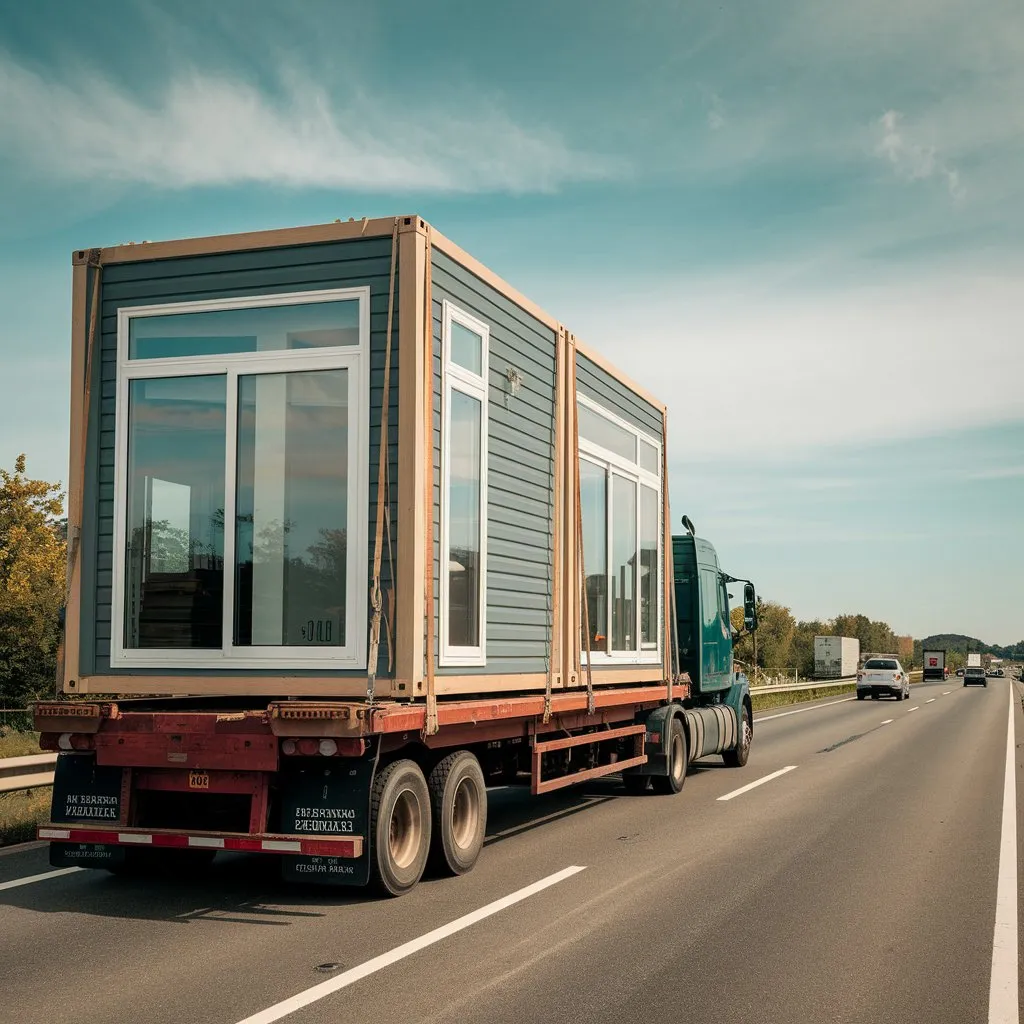
Strategies to Optimize Modular Home Costs
- Simplify the Design: Opting for a more straightforward layout with standard finishes can help keep engineering and manufacturing costs lower.
- Select Cost-Effective Materials: There are budget-friendly materials that still offer quality and durability. For example, using engineered wood instead of solid hardwood can save on flooring costs without sacrificing appearance.
- Compare Manufacturer Quotes: Requesting quotes from multiple reputable manufacturers can help identify competitive pricing and potential savings.
- Prepare the Site in Advance: Ensuring that the site is graded, accessible, and has necessary permits before installation can reduce delays and additional expenses.
Conclusion
Modular homes present an efficient and customizable alternative to traditional housing, but understanding the detailed cost breakdown is crucial for making informed decisions. By examining each component—from materials to installation—buyers can assess the value of modular construction and determine how to meet their budget and preferences. Whether building a small starter home or a custom luxury residence, modular homes can offer excellent value with careful planning and strategic choices.
1 thought on “Analyzing the Costs of Modular Homes: Breaking Down the Total Expense Components”